Here are a few examples of design work I have done over the years:

This was a fun little project. The customer had a very old bottle opener with the company brand name on it and wanted to make a new version. This was a very simple job--just reproducing the outer shape of the original, then updating and modifying their branding text so it could be produced easily. Laser cut steel.
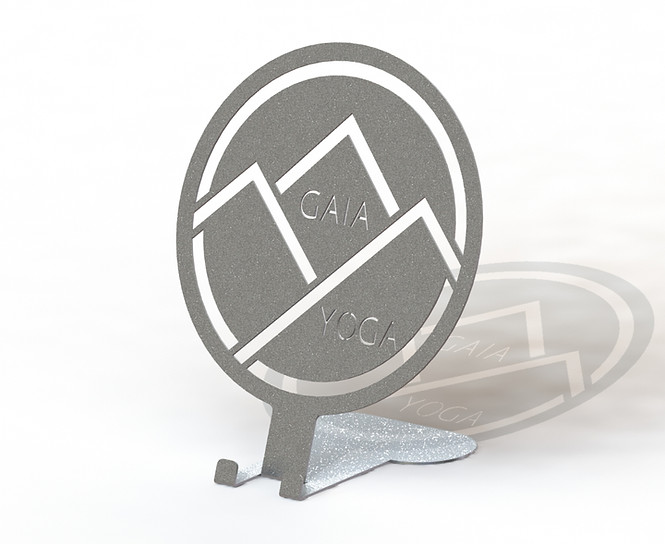
This is a business card holder for a company’s front desk. I have done quite a few versions of these now for my local fabrication shop. It’s fun to come up with a nice way to show a company’s logo in metal (just cuts, no color). More art than engineering. Laser cut/fabricated aluminum.

This is one example of a whole line of products that I have been working on with a customer. Shown is a bracket with pre-mounted water supply lines, to make installation of plumbing faster and easier. I think this is a great idea, and it is moving on to production levels of manufacture as I write this. Fabricated galvanized steel, integrated with various purchased parts.

This was a fun product. It’s a simple wire-formed holder, designed to hold food items not ordinarily put in a pop-up toaster—brand name Toastilla. The inventor had the basic form of the wire figured out, and I worked with him to design the handles for injection molding when in production (we did 3D prints first). I made a few prototypes in my shop. Wire-form stainless steel, and injection molded plastic.

This is a very small part of a much larger industrial project, but one that was interesting, because it had so many design constraints. Shown is the end on a manipulator arm, which extends and retracts, and is able to “grasp” a piece of foam material by extending the corkscrews. Once the material is picked up, the mechanism can rotate axially 90 degrees, and “knuckle” 90 degrees. All of this had to be accomplished in a package which is 1” x 1” when retracted and viewed from the end. It could not have power to it because of a wet environment, so it is all pneumatic. I did a 2” x 2” version as well, but that was easy after this. Machined aluminum, PTFE and stainless steel, and fabricated stainless steel.

This is a set of adjustable triple clamps for a motorcycle. The customer had made many similar clamps, but these were a new and more complicated design. He needed help determining the details of the design, and how much adjustability was necessary to achieve the results wanted. Making detailed computer models saved him a lot of time and money vs. his making lots of prototypes. All machined aluminum.

This is a large, industrial rotary die station done for a large corporate client. This project was all about RIGID. The main ribs on this unit are 1.5” and 2” thick steel, with lots of interlocking machined parts. Two inline die stations, and an input and separate output nip drive--so four separate drive motors. The picture on the bottom shows the die station with the supply roll on its stand and with the safety cage in place. I did all of the Solidworks model and design on this, as well as the very complicated dies themselves (they remain proprietary, so can’t be shown). Machined steel and aluminum, including large turned parts, plastic, rubber, fabricated steel and aluminum.

Pizza Truck! This was an interesting one, a fully automated food truck that served pizzas. I was the lead engineer on this project. The pizza was stored in a refrigerated section, and moved through one of four high-speed electric ovens that cooked them in about a minute. The ordering and payment were done through iPads. Lots of software/hardware interaction on this project, and all power was supplied from batteries mounted in the truck chassis. Soda fountain stations in there too!
This was a large industrial machine developed for a large packaging corporation. It is an automated foam fabrication system. The video shows two layers of foam being laminated together, cut with a water-jet, then re-positioned and handed off to another section where they are heat-bonded to the remaining parts. This was an early test of the machine; in production it would be performing all of these actions on 12-16 parts at a time, not just one as shown. Designed from the ground up, using an aluminum extrusion framing system and LOTS of servo-controlled movement, pneumatic control, and integration of water-jet cutting heads.